Kanban – A Guide to Organizing Projects & Work
Looking to maximize your team's productivity and speed of software delivery? This comprehensive guide to Kanban provides expert insights on optimizing workflow, improving agility, and achieving continuous improvements through an elegant visual management system.

Kanban is a visual project management system that originated from Toyota's production system and is now a popular agile framework.
This article provides a comprehensive overview of Kanban and its practices to help teams implement Kanban successfully. It covers the Kanban board, work in progress limits (wip limit), continuous flow, incremental improvement, and metrics tracking.
By the end, you'll understand the benefits of Kanban and be able to decide if it's the right approach for your team.
Key Takeaways
- Kanban utilizes a visual board to showcase the workflow and limit work in progress
- The focus is on improving flow efficiency and finishing existing work faster
- Kanban encourages continuous, evolutionary change rather than dramatic transformations
- Key metrics like cycle time and lead time are tracked to optimize workflow
- Kanban promotes communication, collaboration, and self-organization amongst teams
- Kanban can be used for knowledge work that is variable and has changing priorities
Understanding Kanban: A Beginner's Guide
Kanban is a visual project management framework that has revolutionized the world of agile software development. Originally developed by Toyota to optimize its manufacturing process, Kanban is now used by software teams globally to deliver software faster with higher quality.
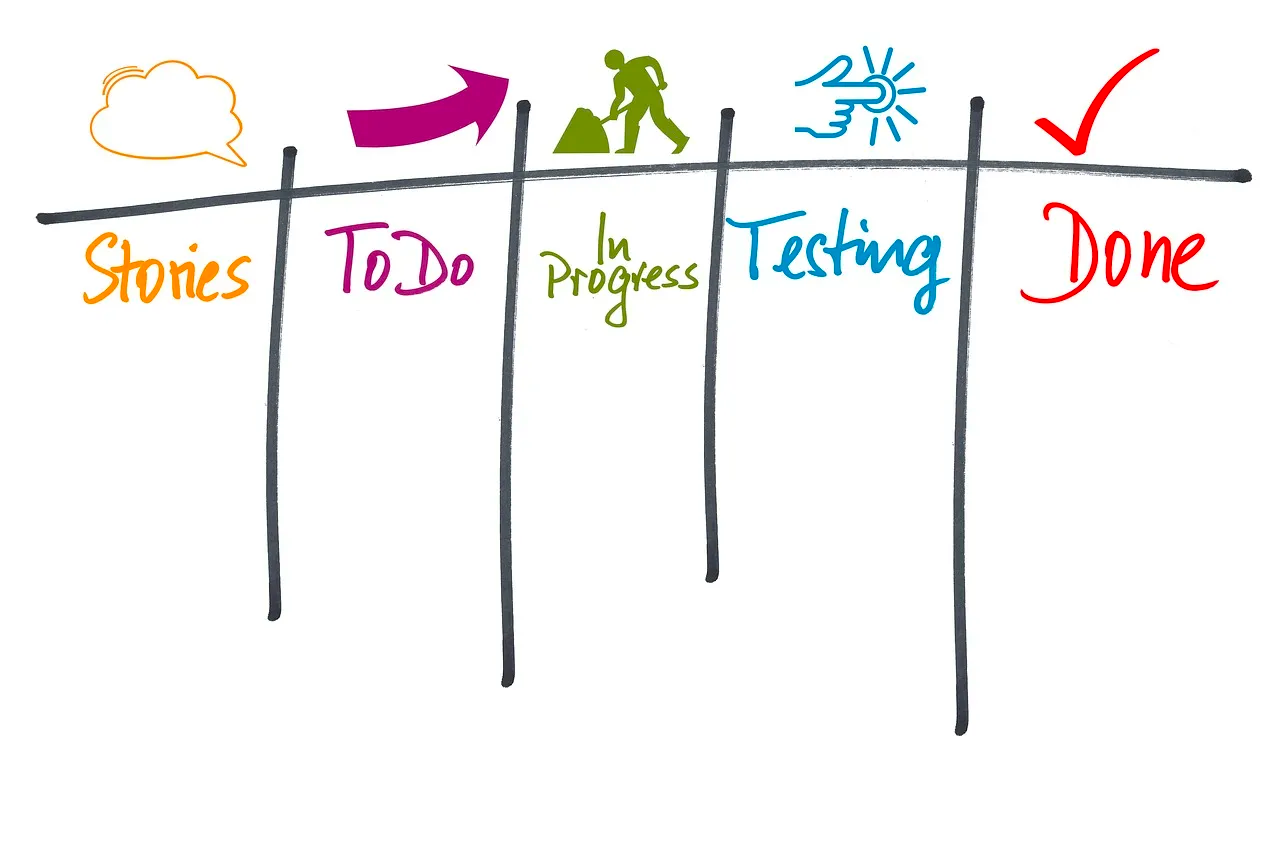
As an experienced agile coach who has implemented Kanban systems at multiple organizations, I'm excited to provide an in-depth overview of this powerful framework. In this guide, I'll share key insights from years of hands-on experience so you can understand the fundamentals of Kanban and how to successfully apply it.
At its core, Kanban leverages visual signals to establish process workflow limits. This transparency helps teams focus on finishing work in progress faster while eliminating bottlenecks. But Kanban is far more sophisticated than just a to-do list on a whiteboard. When fully implemented, it is a holistic system that facilitates agility, collaboration and continuous improvement.
Let's start by examining the foundational principles and practices that make Kanban such an effective agile framework.
What is Kanban?
Kanban is a workflow management method designed to help teams work together more efficiently. The overarching goal is to create a smooth, predictable flow of work to get things done incrementally without overburdening team members.
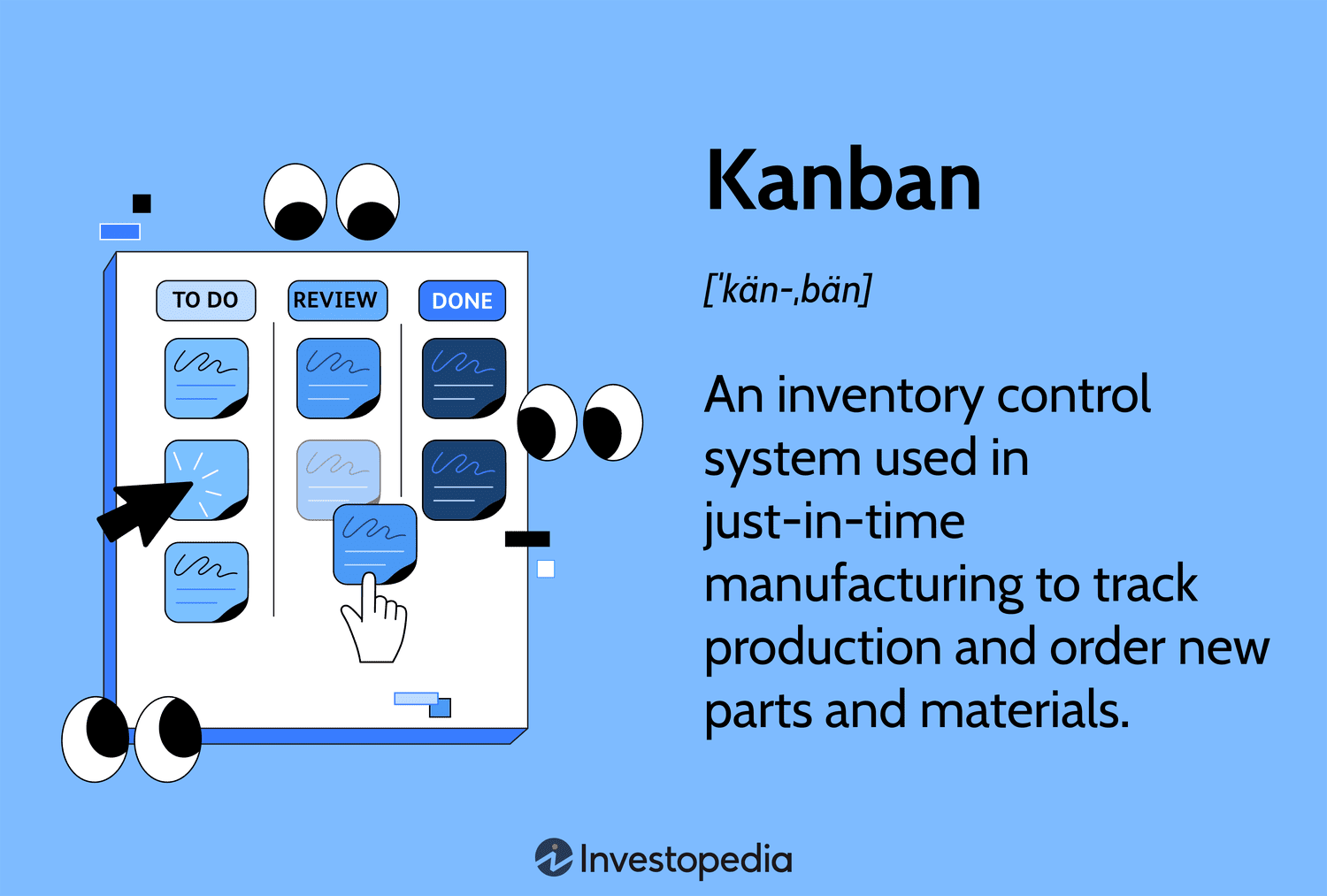
Unlike waterfall approaches where each step must be completed before the next begins, Kanban allows for multiple tasks to be in progress simultaneously. However, there are mechanisms to ensure work doesn't pile up and cause issues down the stream.
Visually, Kanban uses a board with columns representing the various states of work from start to finish. Work items or "cards" move across the columns as tasks get completed. The board provides real-time visibility into what's being worked on and where issues or blockers exist.
Some of the key principles of Kanban include:
- Visualize Workflow
The Kanban board visually represents work stages and progress so that everyone understands the process. - Limit Work In Progress
Setting work in progress (WIP) limits prevents team members from taking on too much at once. - Focus On Flow
The goal is to optimize flow of work across the board, not maximize individual utilization. - Continuous Improvement
The team continuously monitors metrics and processes to identify areas for improvement through kaizen (change for the better). - Empower Team
The team is involved in designing and evolving processes to take ownership of achieving optimal flow.
Now let's dive into the mechanics of Kanban starting with constructing and using a Kanban board.
The Kanban Board
The Kanban board is the central, visual hub that provides transparency into workflow and current work items. While physical boards using sticky notes are popular, virtual boards in tools like Trello are also common.
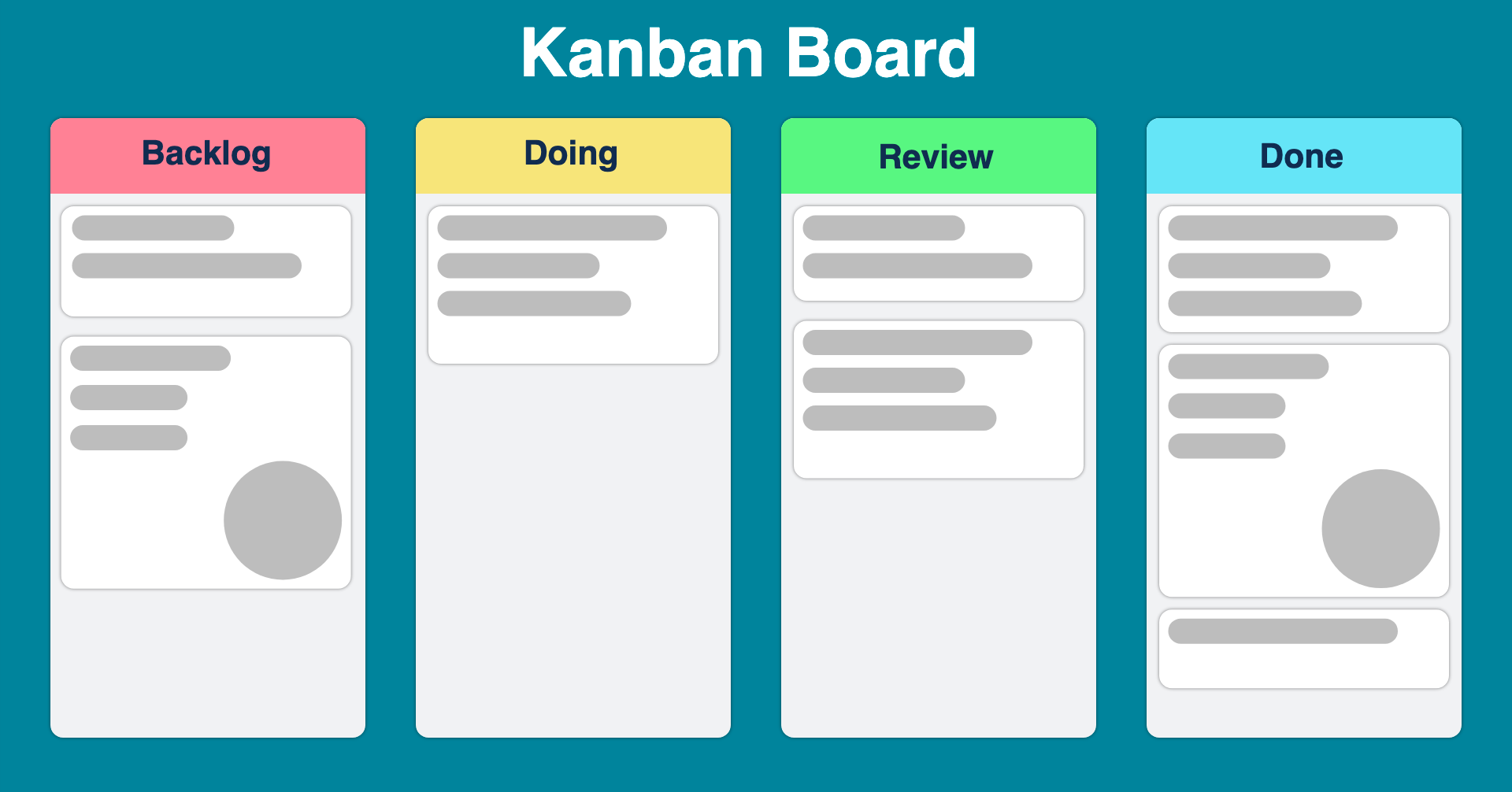
Here's how to create a simple Kanban board:
- Split into horizontal columns for each state of work: To Do, In Progress, Complete
- Split into vertical swimlanes to divide work by type, owner, class of service
- Add cards to represent work items, features, or tasks that move across columns
- Limit number of cards in each column based on team capacity
- Use colors, categories, icons to distinguish classes of work
The board evolves based on the team's needs. More columns can be added for various work stages. Stylistic choices like color coding classes of service help prioritize and classify work.
Some other boards have more advanced workflows with multiple stages under "In Progress" and "Done" columns. The key is crafting a board that maps to your process. As you use the board, refine it to better visualize how work flows through your system.
Now let's look at some best practices for getting the most from your Kanban board.
Implementing Kanban
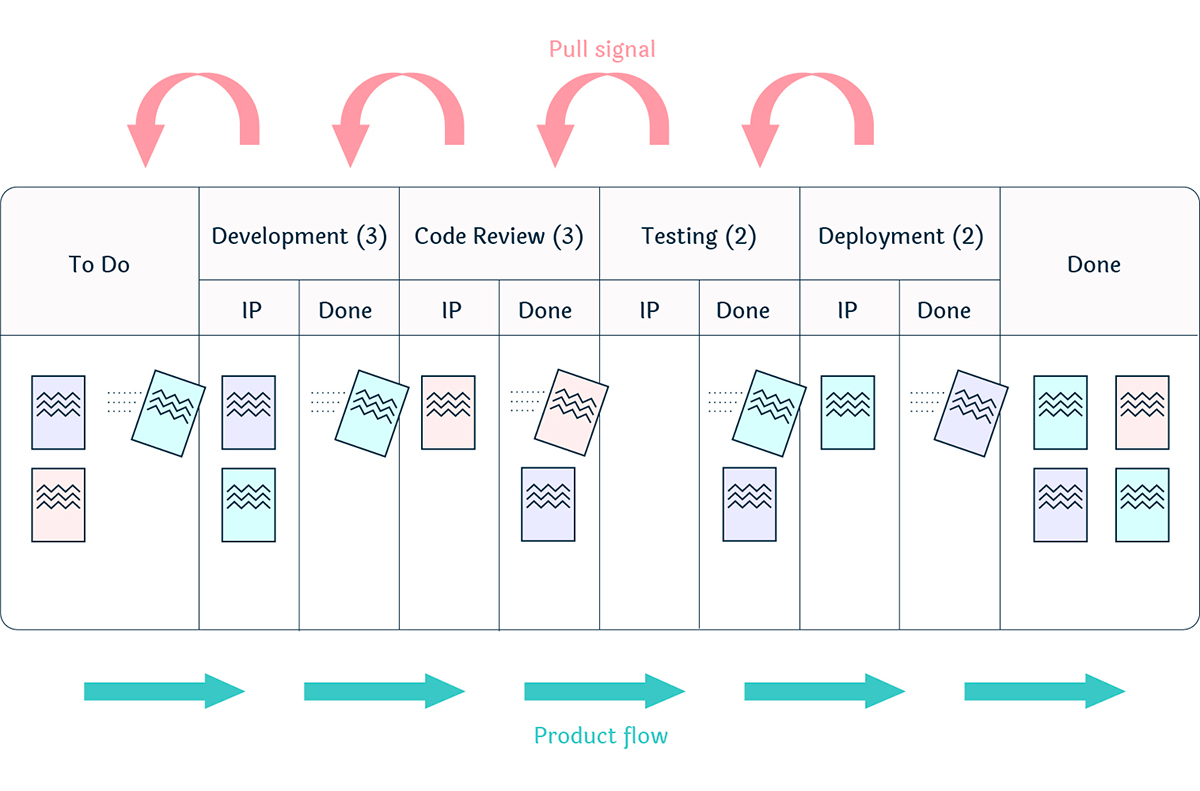
Here are some tips for effectively implementing Kanban:
- Start with your existing workflow - Kanban integrates with your current process
- Involve the team in designing the board - increased buy-in and understanding
- Focus on improving flow before anything else - avoid early optimization
- Start with WIP limits of 1-2 items in each column - tighten over time
- Add new columns gradually - only add when there's a clear need
- Regularly review metrics like cycle time and flow rate - tweak process to optimize
- Conduct regular retrospectives to share feedback and ideas
- Automate cards moving across columns to maintain real-time accuracy
- Update board throughout day vs set "ceremonies" - fluid, real-time transparency
- Pair Kanban with other agile practices like standups and continuous integration
The beauty of Kanban is that starts with your existing approach and evolves from there. By adopting continuous, incremental improvements, you avoid major disruptions to operations. Over time, the cumulative effect of small enhancements leads to substantial optimization.
Now let's discuss some core principles for making the most of Kanban.
Kanban Principles
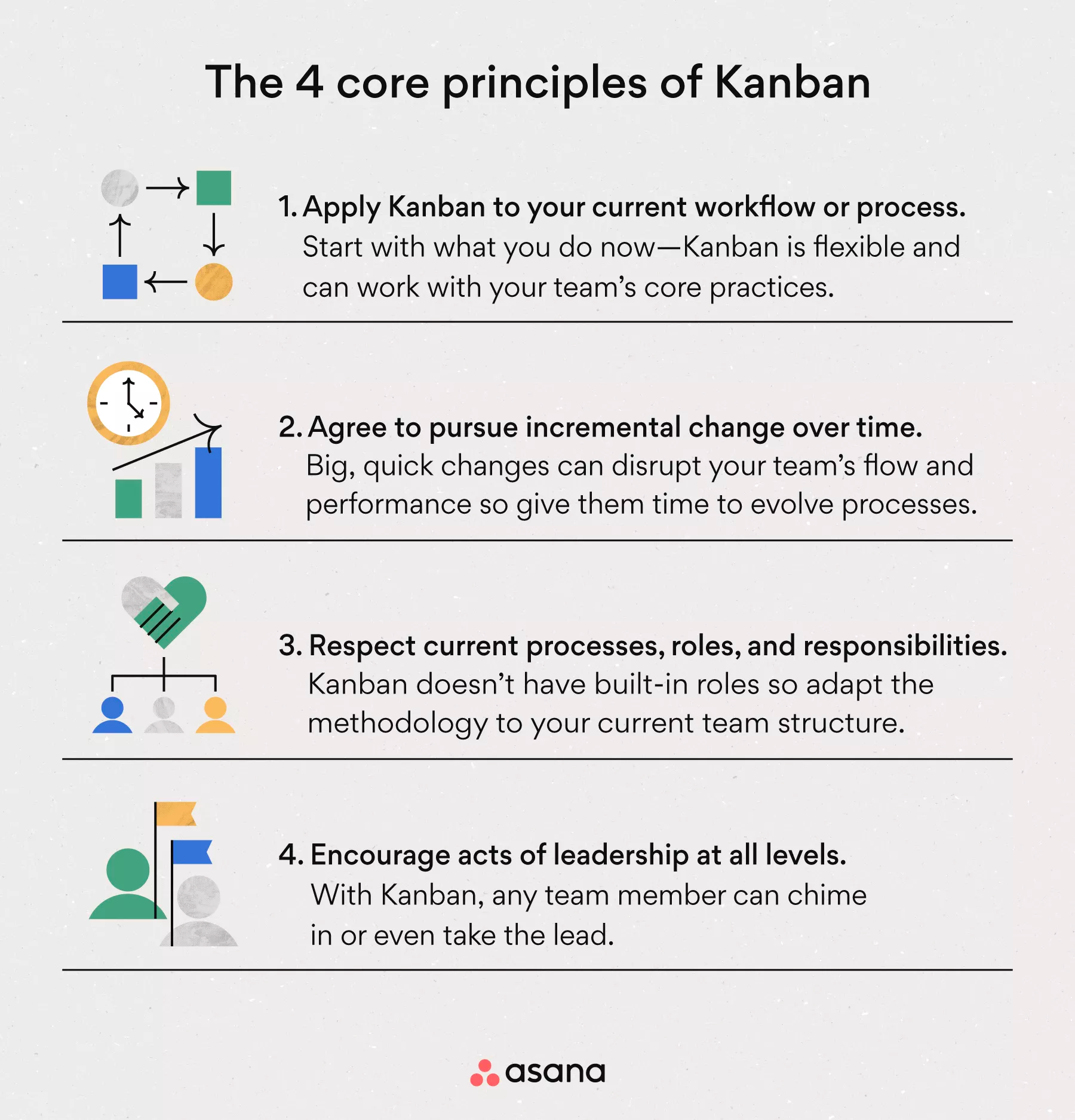
Here are several guiding principles for implementing Kanban effectively:
- Start with existing approach - initially respect current roles, responsibilities, and job titles
- Pursue incremental evolutionary change - small enhancements accumulate into substantial improvement
- Promote transparency - the board and metrics provide visibility into progress and blockers
- Foster collaboration - daily standups in front of board builds shared understanding
- Develop metrics based process improvements - data-driven analysis and decision-making
- Encourage acts of leadership at all levels - input and initiative from entire team
Following these principles sets up a culture of continuous improvement driven by transparency and team engagement. As the Kanban system evolves, so will processes, policies, working agreements, and eventually team member responsibilities. Kanban provides the framework for this growth.
Key Benefits of Kanban
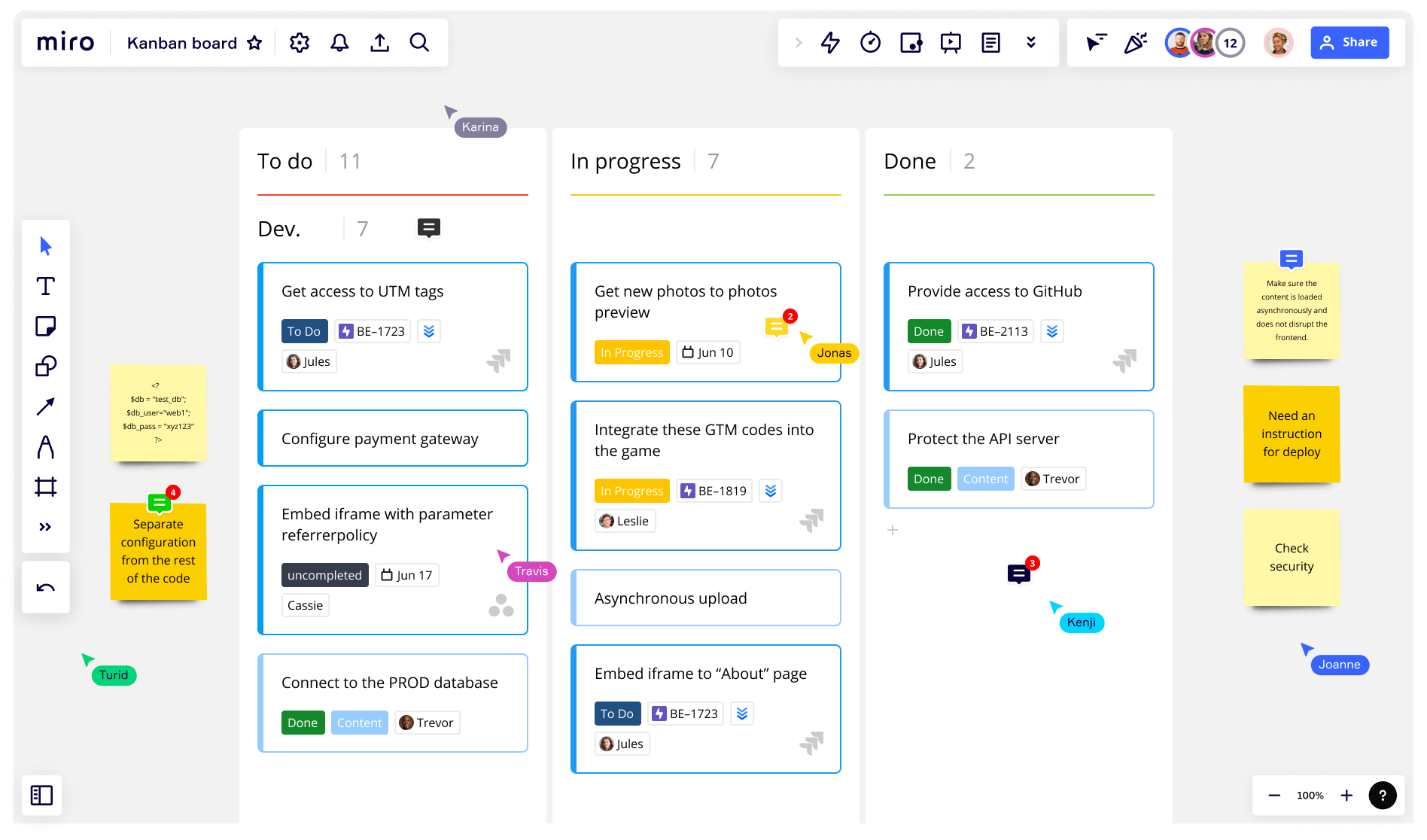
What makes Kanban so popular among agile teams is the tangible benefits it provides:
- Improved visualization of work items and workflow constraints
- Reduced cycle times by focusing on finishing started work before starting new
- Better prioritization based on classes of service and work-in-progress limits
- Increased communication, collaboration and shared understanding amongst team members
- Finding and addressing bottlenecks rapidly due to real-time flow metrics
- Promotion of continuous, evolutionary improvement through kaizen
- Reduction in waste and inefficiencies related to overburdening resources
- Ability to self-organize and optimize flow with a pull-based system
Kanban provides the visibility to identify issues and the flexibility to address them incrementally. Together, this leads to leaner, more adaptive teams.
When to Use Kanban
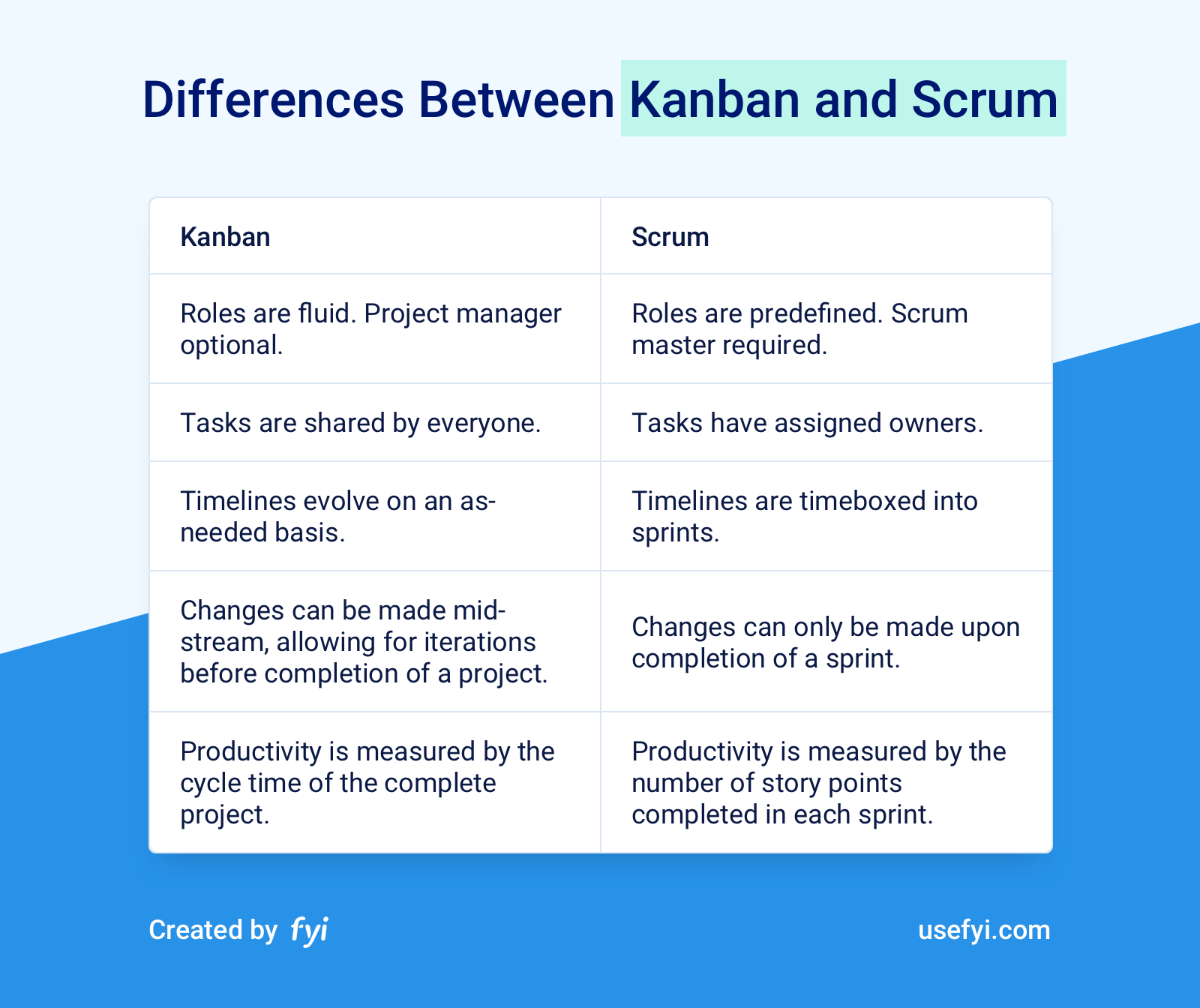
Consider using Kanban in these scenarios:
- Your requirements frequently change
- Your team needs to adapt to changing priorities
- Cross-functional collaboration is required
- There is lots of unplanned work
- Work items vary in size and unpredictability
- The team wants to continuously improve
- There is a need to see where bottlenecks exist
The visual nature and continuous flow in Kanban make it well-suited for these situations of variability. It allows teams to keep up with changing demands while constantly optimizing.
Conclusion
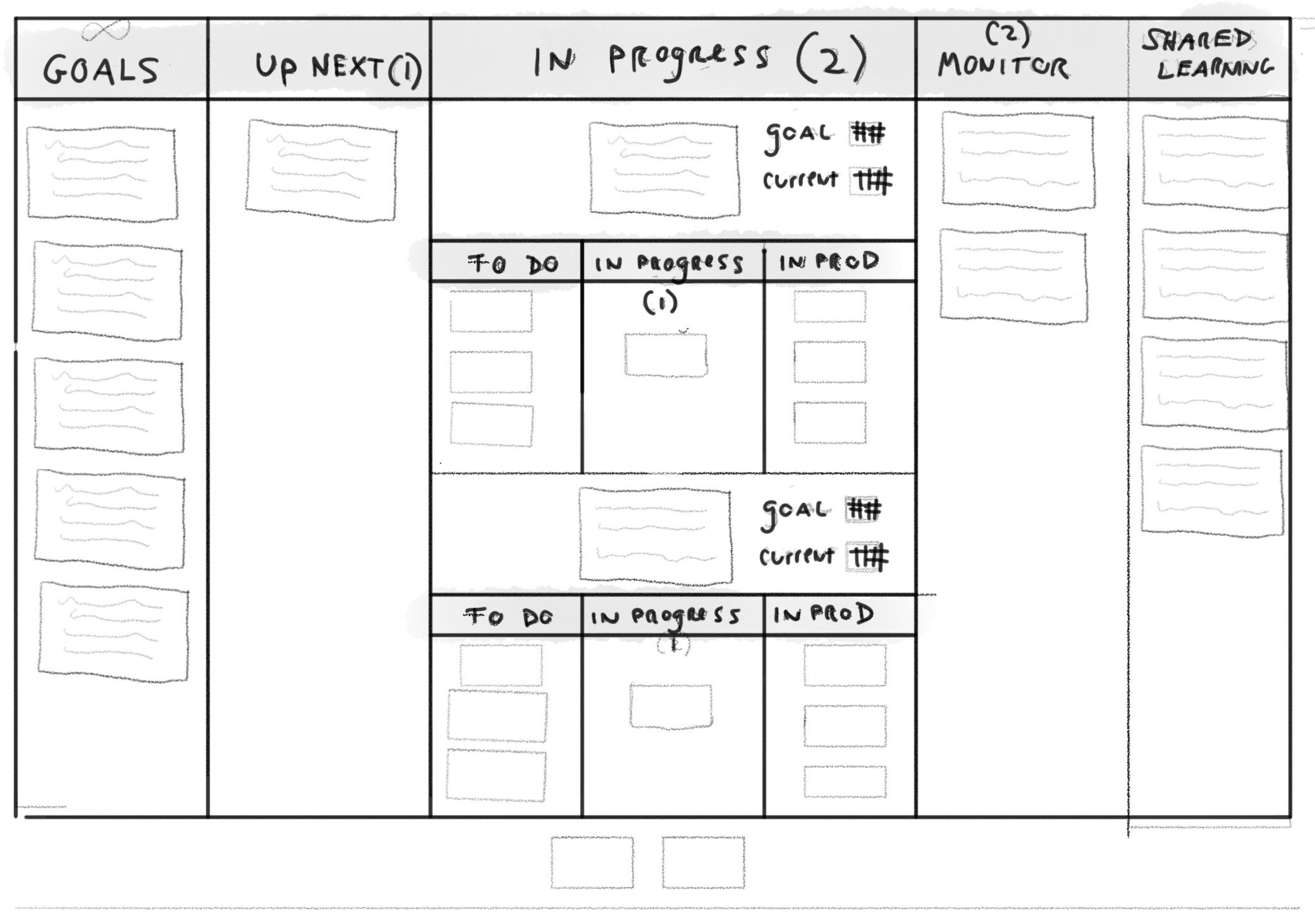
Kanban offers an elegant way to visualize work, limit work-in-progress, and drive continuous improvement. By starting small and evolving gradually, your team can realize substantial benefits. The transparency, discipline, and metrics focus fundamentally improves how work gets done.
While introducing basic Kanban may be simple, mastering Kanban is a journey. This overview provides the foundation and key insights to start that journey. The benefits for teamwork, productivity, and software delivery can be immense.
Whether you're an engineer, manager, project manager, or agile coach, I encourage you to give Kanban a try on your next project. You may be surprised by what a profound impact its principles and practices can have.
Frequently Asked Questions
What are the 6 rules of kanban?
- Visualize the workflow - Use a kanban board to map out the process steps and flow of work. This gives transparency into the process.
- Limit work in progress - Set limits on how much unfinished work can be in progress at each step of the workflow. This prevents overloading.
- Focus on flow - Keep items moving through the workflow smoothly from start to finish. Avoid blockers and bottlenecks.
- Continuous improvement - Reflect on what's working and what isn't to identify opportunities for improvement. Adjust the process as needed.
- Make process policies explicit - Document the rules, policies, processes and expectations so that everyone is clear on how the system operates.
- Implement feedback loops - Get regular feedback from team members on what's working and what isn't. Communicate on a regular basis.
The key is to start small, experiment with changes, and continuously evolve your kanban process based on what works best for your team. The goal is to achieve smooth, effective flow to deliver work efficiently.
What are the 4 principles of kanban?
The four core principles of kanban are:
- Visualize the workflow - Kanban utilizes a visual board with columns representing the different states of work to allow teams to see the flow of work. This gives transparency into what work needs to be done and where issues or blockers may exist.
- Limit work in progress (WIP) - Kanban recommends limiting the amount of work in progress for each state on the board. This prevents overloading and promotes focus on finishing existing items before starting new ones.
- Manage flow - The focus is on the flow of work across the board. Teams actively monitor cycle time, throughput, and other metrics to identify and address bottlenecks or problems impeding flow.
- Continuously improve - Kanban is based on continuous improvement. Teams are encouraged to suggest ideas for improving work efficiency, process issues, or blockers. The goal is to incrementally improve how work flows through the system.
The key is to start visualizing your workflow, set WIP limits, pay attention to flow, and look for small improvements. Following these four principles helps teams gain more predictability, better quality, and improved efficiency with their work.
What is kanban best for?
Kanban is best suited for teams that need flexibility and agility in how they manage work. Specifically, kanban is most applicable in these scenarios:
- Unpredictable or changeable work - Kanban accommodates changing priorities and new tasks seamlessly by allowing teams to add new items onto the board at any time. This makes it a great fit for teams dealing with a dynamic or fast-moving workplace.
- Focus on just-in-time delivery - The work-in-progress (WIP) limits promote completing work only when it's ready to be handled. This just-in-time approach reduces excess inventory or overload.
- Cross-functional teams - Kanban boards can capture the workflow for an entire value stream spanning different teams, functions, or departments. This provides end-to-end visibility.
- Need for visibility and process improvement - The visual nature of kanban boards provides great transparency into current work state and flow. This visibility enables continuous improvement through metrics, activity analysis, and problem-solving.
- Maintenance & support work - The flexibility of kanban is useful for managing open-ended service work like IT tickets, engineering maintenance, customer support cases, and more.
- Project-based knowledge work - Kanban works for projects, especially those with rapidly changing scopes and priorities. The board can easily accommodate new project work.
Kanban shines for teams that need a straightforward system to visualize and manage work with agility, flow, and transparency. The visual board and focus on improvement make it a great lean project management approach.
What are the 5 elements of kanban?
The 5 core elements of kanban are:
- Visual Signal - The kanban card is a visual signal that represents a work item or task. It allows you to see the status of work at a glance.
- Limit Work in Progress (WIP) - By limiting how much unfinished work can be in progress, you prevent overloading the system.
- Focus on Flow - The goal is to keep work items moving smoothly through the workflow from start to finish.
- Continuous Improvement - Kanban method encourages incrementally evolving the process through feedback andmetrics.
- Respecting Current Roles & Responsibilities - Kanban method doesn't require major reorganization. It starts with your existing roles and processes.
The kanban method revolves around these 5 elements to help teams visualize their work, maximize efficiency, and continuously improve. The visual nature of the kanban board allows teams to gain transparency into workflow constraints. By limiting WIP, focusing on flow, and optimizing as you go, kanban helps balance demand with capacity and move work through the system.
What's the difference between kanban and scrum?
The main differences between kanban and scrum are:
- Cadence - Scrum prescribes regular fixed length sprints (e.g. 2 weeks) as well as other ceremonies like planning, retrospective, etc. Kanban is continuous flow-based, without prescribed cadences.
- Roles - Scrum has distinct roles like Scrum Master and Product Owner. Kanban doesn't have formal roles.
- Process - Scrum follows a specific process with set activities. Kanban focuses more on the workflow visualization and limits.
- Releases - Scrum teams work towards fixed sprint deliverables. Kanban teams are not bound to fixed releases and can continuously deliver.
- Planning - Scrum has structured sprint planning sessions. Kanban planning is continuous along with work.
- New work - Scrum locks down scope for a sprint. Kanban allows adding new work onto the board as capacity permits.
- Metrics - Scrum metrics are more tied to sprint goals and velocity. Kanban metrics focus on flow, cycle time, and throughput.
- Change philosophy - Scrum accommodates change between sprints. Kanban embraces constant incremental change through kaizen.
Scrum provides a structured time-boxed framework while Kanban is more flexible without timeboxes. Scrum is better for predictable work while Kanban is better for changing priorities.
Is Kanban Lean or Agile?
Kanban can be considered both lean and agile:
- Lean - Kanban is based on many lean principles including visualizing workflow, limiting work in progress, improving flow, and continuous incremental improvement. The focus on waste reduction, efficiency, and optimizing flow makes kanban a lean methodology.
- Agile - Kanban follows the values and principles behind the Agile Manifesto including focusing on individuals over processes, delivering working product, and responding to change. The fluid and flexible nature of kanban aligns with agility.
Some key reasons why kanban methodology is considered both lean and agile:
- Focus on just-in-time delivery and reducing excess inventory (lean)
- Continuous flow of work with work-in-progress limits (lean)
- Incremental improvements through kaizen (lean)
- Self-organizing teams that pull work on the kanban board (agile)
- Adapting to changing priorities and new work (agile)
- Delivering often with a continuous flow (agile)
The Kanban Method is essentially an agile approach that leverages many lean concepts to improve flow efficiency. The combination of agile and lean makes it uniquely situated in between both methodologies, though still distinctly part of the agile family. Teams adopt it to gain the benefits of visibility, adaptability, and continuous improvement. Agile methodology is mostly a set of concepts and not a process in itself.
When should you not use Kanban?
There are a few situations where Kanban may not be the best choice:
- For projects with fixed deadlines or rigid time constraints - it works best with flexible delivery timelines based on a continuous flow of work. If you have inflexible deadlines, other methodologies like critical path or waterfall project management may be preferable.
- When requirements are not clear - Kanban Method relies on breaking down work into well-defined pieces that can flow through the process. If requirements are vague or unclear, it can be difficult to create Kanban cards and visualize workflow.
- No buy-in from team members - In order for Kanban to work, the team must follow the process. Without full buy-in and commitment from members, Kanban boards can be ineffective.
- Team members lack autonomy - Self-organizing teams that can pull new work as capacity allows are key for Kanban. It won't work well in top-down structures with no team empowerment.
- When there is no process to improve - Kanban shines at incrementally improving an existing process. If no process currently exists, Kanban may not be the place to start.
- Need complex statistical forecasting - Kanban's simple metrics like cycle time and throughput may not provide the advanced forecasting some projects require.
The key is to match the methodology to the type of work, project environment, and team culture. Kanban can deliver great value in the right circumstances, but isn't a universal solution for all situations.
Is Kanban outdated?
No, Kanban is not considered an outdated methodology. Here are some reasons why Kanban is still relevant today:
- Growing adoption - Kanban adoption in organizations continues to grow year over year, indicating it is gaining more mainstream acceptance.
- Visualization - The visual workflow focus of Kanban is becoming more important as organizations adopt complex workflows. Visualization provides clarity.
- Flexibility - Kanban's flexibility works well with today's dynamic business environments compared to more prescriptive methods.
- Flow focus - The emphasis on work-in-progress limits and continuous flow matches the needs of modern engineering and operational teams.
- Lean connection - Kanban's lean principles are still central in today's focus on agility, efficiency and waste reduction.
- Evolution - The Kanban method continues to evolve through communities of practice and guides, adding new techniques.
- Online tools - Digital Kanban boards and software tools make implementation accessible compared to traditional manual boards.
- Teaming - Kanban fits with the shift towards cross-functional teams vs specialized silos.
While Scrum is still more widely used, Kanban fills an important niche for teams that need more flexibility. The combination of lean and agile in Kanban will ensure it remains a relevant option moving forward. Rather than being outdated, Kanban continues to prove its usefulness in the modern workplace.
Why does Kanban fail?
Kanban can fail or not deliver results when implemented incorrectly. Here are some common reasons for Kanban failure:
- Lack of management support - Without management actively supporting Kanban, teams won't have authority to make changes.
- Poor training - Team members need proper training on Kanban principles and practices to follow basic principles correctly.
- No workflow analysis - Not spending time to map out workflow leads to poor board design that doesn't reflect reality.
- Adding Kanban mid-project - Kanban works best when applied from project/workstream outset rather than tacked on mid-way.
- Ignoring WIP limits - If teams don't enforce WIP limits, work will continue to pile up causing flow issues.
- No metrics tracking - Not measuring cycle time, throughput etc means there's no way to improve.
- Rigid processes - Trying to force-fit Kanban without adapting processes causes resistance.
- No continuous improvement - The board becomes static without making incremental workflow changes to the production process.
- Cultural resistance - Lack of buy-in and resistance to change hampers Kanban adoption in development teams.
- Board not updated - If the board isn't updated frequently, it loses value becoming obsolete. Lack of access to online kanban boards will also cause issues for the development team.
The key is proper preparation, training, leadership buy-in, and culture adaptation for software development teams to thrive. When implemented correctly with the right foundations, Kanban can deliver great results.
Additional Questions
What is a kanban system?
A kanban system is a workflow management method that uses visual signals to control the movement of work across a value stream. It originated from lean manufacturing practices at Toyota. The goal of a kanban system is to create an efficient workflow by limiting work-in-progress, exposing bottlenecks, and facilitating continuous improvement.
What are some common kanban practices?
Some key kanban practices include:
- Visualizing workflow on a kanban board
- Limiting work-in-progress with constraints
- Continuous flow of work from start to finish
- Making process policies explicit
- Improving collaboratively and incrementally
Properly implementing these kanban practices will help create a smooth flow of work.
How are electronic kanban systems used?
Electronic kanban systems allow teams to visualize workflow and update work status on a digital board rather than a physical board. This makes kanban practices easier to implement through features like cards, columns, swimlanes, and WIP limits. Electronic kanban systems help automate workflows, especially in software development environments.
What is the connection between kanban and the Toyota Production System?
The Toyota Production System pioneered concepts like just-in-time manufacturing and jidoka which aim to eliminate waste in production processes. Kanban was developed as a scheduling system to implement these lean principles on Toyota's production lines. So the Toyota Production System provided the foundation for kanban.
When should service request managers consider using electronic kanban systems?
Service request managers handling tickets, cases, or incidents can benefit from implementing electronic kanban systems. The workflow visualization and limiting of work-in-progress can help smooth flow and prevent bottlenecking. This leads to faster service delivery, better cycle times, and improved customer satisfaction.
How does kanban apply to knowledge work and business processes?
While kanban originated in manufacturing, it is now being used to optimize knowledge work that involves business processes like product development, marketing, IT, and more. Kanban provides visibility into ambiguous workflows, limits multi-tasking, and promotes completed work. This lean approach to intangible work brings efficiency and predictability.